Factory and Warehouse
Product Form
Ductile Iron Pipes All Types:
1 |
Material |
Ductile Cast Iron |
2 |
Joint Type |
T-Type(push-on joint) |
K-Type(Mechanical Joint) | ||
Self-Restrained | ||
Flanged joint | ||
3 |
Standard |
ISO2531, EN545, EN598, etc |
4 |
Size |
DN80 - DN2600 (80mm - 2600mm) |
5 |
Classs |
K7, K8, K9, C40, C30, C25, etc |
6 |
Length |
6m, cut to 5.7m |
7 |
Internal lining
|
1. Portland cement mortar lining |
2. Sulphate Resistant cement mortar lining | ||
3. High-Aluminum cement mortar lining | ||
4. Epoxy Resin Lining | ||
5. Epoxy Ceramic Lining | ||
6. PU Lining | ||
8 |
External Coating |
Zinc+bitumen coating, |
Customized coating such as Zinc-Epoxy, Alumina Powder, PU, FBE, Epoxy-Ceramic, etc. | ||
9 |
Rubber Gasket |
NBR rubber, SBR rubber or EPDM rubber ring as per ISO4633 |
10 |
Application |
Potable Water / Drinking Water/Sewage Water |
11 |
Packing |
DN100-DN300 in bundles; DN350-DN2600 in bulk ship |
Introduction
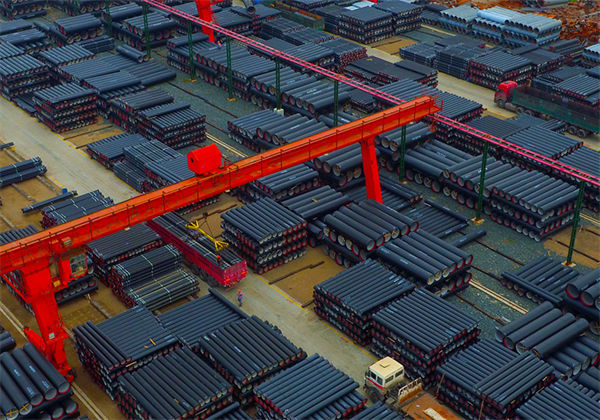
Our Ductile Iron Pipe EN 598, the epitome of excellence in water transportation. Engineered with precision from high-quality ductile iron material, these pipes are designed to meet and exceed EN 598 standards, ensuring optimal performance and durability.
Our Ductile Iron Pipe EN 598 is specifically crafted to handle the demands of water and wastewater conveyance with ease. Its robust construction allows it to withstand high pressures, heavy loads, and harsh environmental conditions, ensuring reliable operation for years to come.
Compliance with EN 598 standards guarantees the highest levels of quality and safety, providing our customers with peace of mind and confidence in their choice. The pipes' corrosion-resistant properties ensure minimal maintenance and a long service life, making them a cost-effective investment.
Versatility is a key advantage of our Ductile Iron Pipe EN 598, available in a wide range of sizes and pressure ratings to suit various applications. Whether it's for municipal water supply networks or industrial projects, our pipes deliver consistent performance and efficiency.
Choose our environmentally friendly Ductile Iron Pipe EN 598 for dependable and sustainable water transportation solutions. Upgrade your infrastructure projects with our top-of-the-line piping solution, setting new standards in water conveyance. Trust in our commitment to quality and experience the excellence of Ductile Iron Pipe EN 598 today.
Benefits of ductile iron pipe
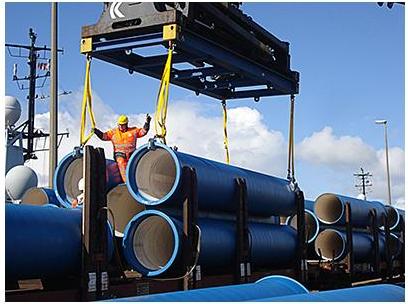
Solid under loads
In underground conditions, the ductile cast iron pipe has a semi-rigid behaviour: it offers an excellent compromise between mechanical stress in the wall (small DN) and ovality (large DN). It can be laid in high and low height of cover, and easily in soil of low rigidity. The ”ground/semi-rigid pipe” system offers optimum mechanical stability over time, without risk of buckling in large DN.
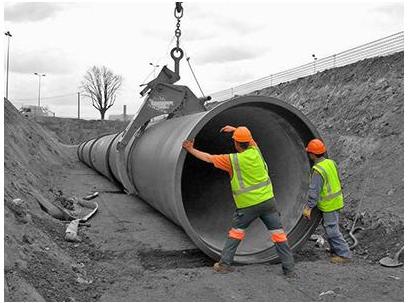
Insensitive impacts
The ductile cast iron structure has a high elastic deformability and a high resistance to crack initiation: it results in excellent impact resistance. The cast iron pipes are perfectly suited to transport conditions over long distances (truck, train or ship), handling conditions on sites and to different types of backfilling. The ductile cast iron pipelines may be laid in very difficult areas: rocky mountain slopes for hydroelectric plants, crossings for cantilever bridges, rockfill for submarine outlets.
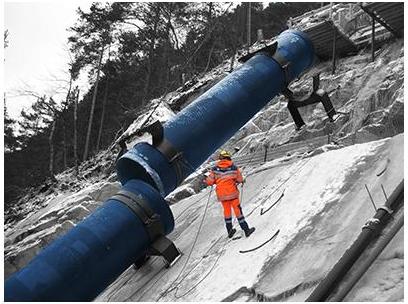
Push-in joint system
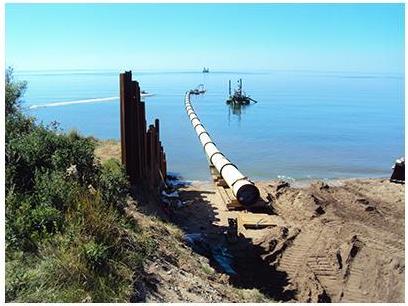
Excellent hydraulicity
The centrifugation process ensures a perfectly smooth and even cement surface. The Colebrook roughness coefficient of an isolated pipe is k = 0.03 mm. We recommend the use of an average value of k = 0.1 mm for sizing networks in order to take into account all the different load losses caused by singular points (tee fittings, elbows, valves, etc.)
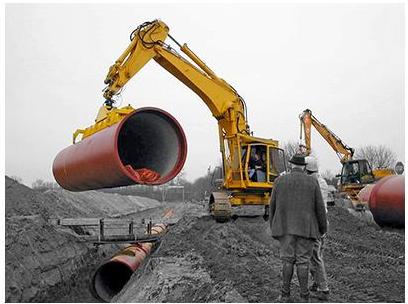
Pressure resistance
The ductile cast iron pipe are designed to withstand pressures much greater than the values usually encountered on the networks. The wall thickness is calculated with a safety factor of 3 with respect to the maximum operating pressure. This additional safety margin is very useful to the impacts during installation, accidental overpressure and mechanical operating fatigue.